数字孪生技术不仅是工业4.0的催化剂,更是智能工业的新篇章。随着技术的不断进步,数字孪生将为传统产业带来革命性的变革,引领我们走向Digital twins
A new engine for industrial upgrading
As the wave of the fourth industrial revolution sweeps the world, digital twin technology is becoming a key force driving industrial innovation.

Digital twin, also known as digital twin or digital mirror, is a virtual technology that enables dynamic simulation of the entire life cycle process of physical equipment through the integration of physical models, sensor data, and historical operating data. Unlike traditional design, digital twins are “live” and can reflect the state of the ontology and external environmental conditions in real time.

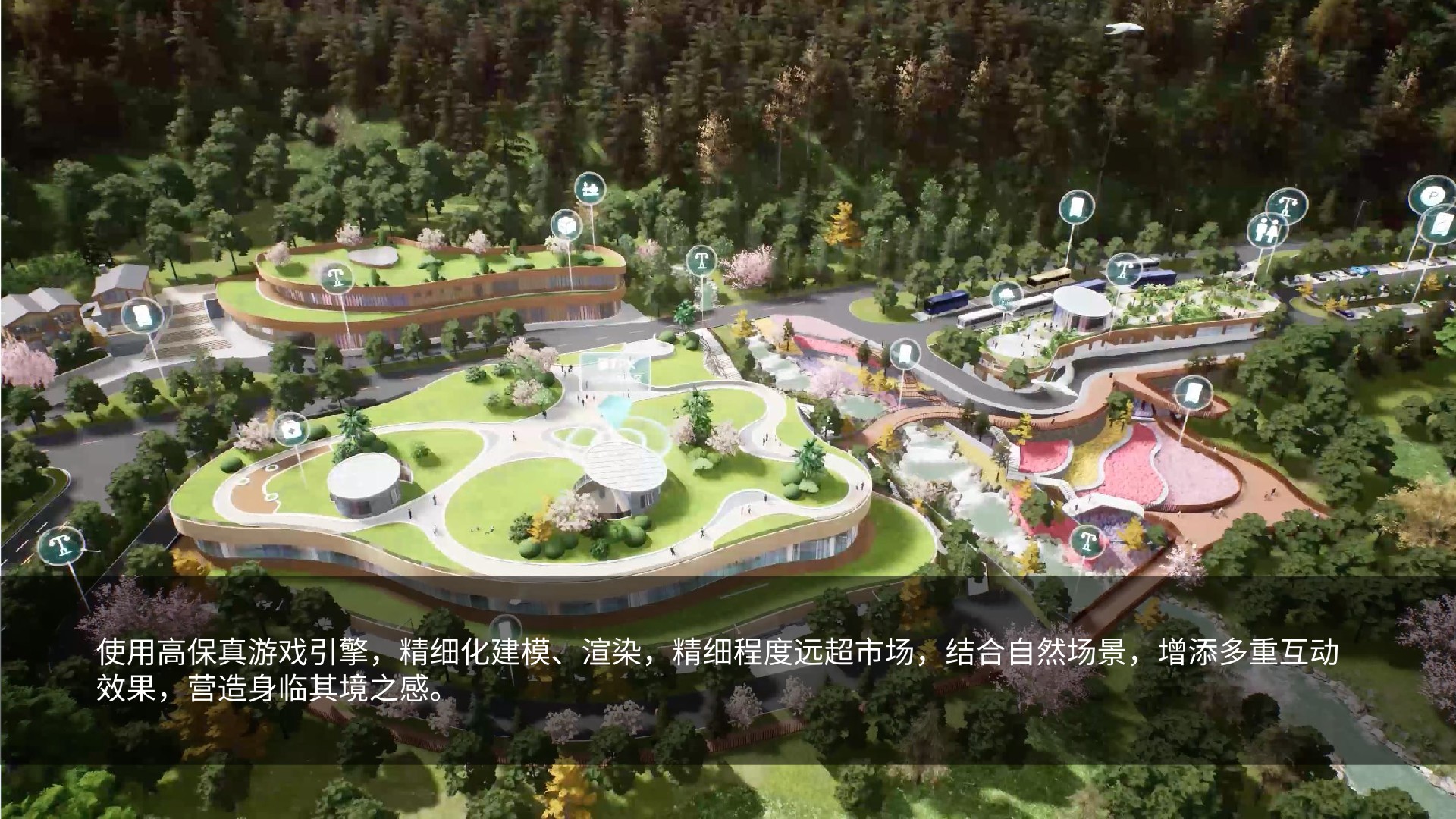
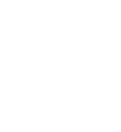
Features of a digital twin
The application of digital twins in the industrial sector
Product development: During the design phase, digital twins can build a digital model of the product, conduct simulation testing and verification, and accelerate the development process.
Manufacturing: Optimize the production process and improve efficiency by simulating the operation of equipment and parameter adjustment.
Predictive maintenance: Through intelligent analysis of operating data, predict the optimal time for maintenance and reduce downtime.
The value that digital twins bring
Improve reliability and availability: Digital twins improve product performance and stability through simulation and testing.
Reduced risk: Experimenting on digital twins avoids the impact on physical products and reduces R&D and manufacturing risks.
Efficiency improvement and cost reduction: The application of digital twin technology has significantly improved production efficiency and reduced operating costs.
Digital twin technology is not only a catalyst for Industry 4.0, but also a new chapter in smart industry. With the continuous advancement of technology, digital twins will bring revolutionary changes to traditional industries and lead us to a smarter, more efficient and sustainable industrial future.
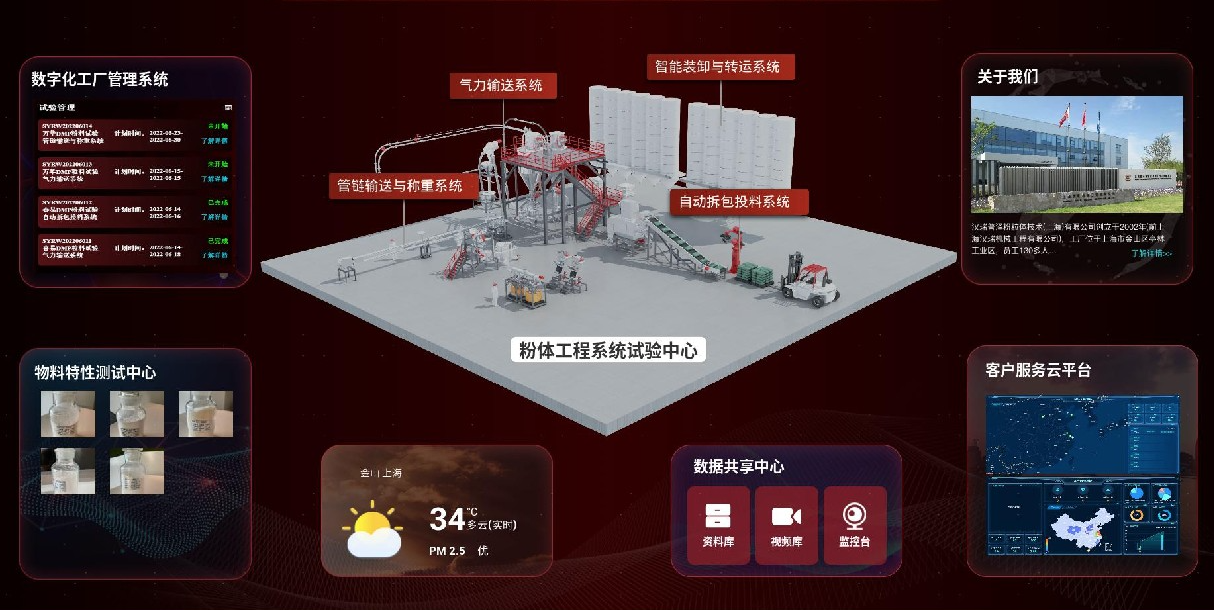
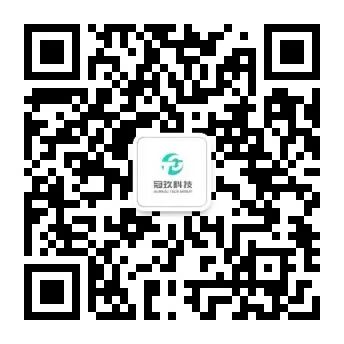